The predictive simulation tool for friction welding
The finite element software virtua RFW is the world’s first simulation tool being able to map the complex physics of the rotary friction welding process (RFW) in a predictive way. With the aid of this software the RFW process is modeled by entering the geometry data of the parent parts and clamping jigs, physical properties of the involved materials and the machine and process parameters. Numerous experimental studies and applications of the software have proven the very good validity of the simulation results, being expressed by an excellent correlation of process parameter runs, plastic deformation shapes and temperature cycles between the simulation and application.
The software virtua RFW assists you in
-
in understanding your RFW processes,
-
working out suitable and innovative designs of the weld parts
in particular their joint geometry, -
studying the effect of the process parameters on the weld
process and performance, -
discovering potential failure modes and quality lacks very early
in the product development process, -
developing new process variants and technologies and
-
illustrating and documenting your friction welding processes.
We continuously improve and develop virtua RFW further, modify it with respect to your requirements and offer services and consultancy for your applications.
Get in contact with us for more information about the software and ways of testing and using it in your organization!

virtua RFW
Under the hood - The CFD-engine of virtua RFW
-
Self-developed, finite element based CFD-engine according to the latest state-of-the-art in numerical analysis
-
Consistently assessed Carreau-fluid constitutive model
-
Exponential decay transition friction law coupled to the constitutive law
-
Mixed explicit/implicit, fully coupled thermo-mechanical solver with automated time step size adaption
-
2.5D axisymmetric formulation of the governing equations
-
Completely automated meshing, mesh monitoring and remeshing using Persson’s implicit geometry meshing routine
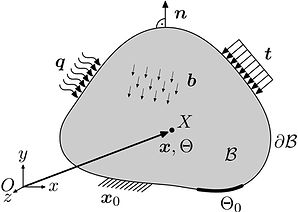

Dynamic viscosity according to Carreau's fluid law
Features of virtua RFW
-
Stand-alone executable software which can be run on a standard PC*
-
Simulation of directly driven, inertia driven and custom parametrized RFW processes
-
Matlab syntax based model definition files providing very good readability and excellent parameterization options
-
Preprocessor application allowing a user-friendly, fast and efficient creation of models including data base management of materials, joint geometries and processes
-
STL format interface featuring direct geometry import from CAD software such as Catia, Solid Edge, Pro/Engineer etc.
-
Processor application with live preview of simulation results
-
Output of customized rendered animation clips, PDF reports and data containers giving complete access to all calculated field variables
-
Comprehensive documentation and handbook
-
Batch mode for automated execution of a multitude of jobs
-
Console mode for easy implementation in third party optimization software
*Intel Core i7 6700K or equivalent with at least 16GB RAM recommended
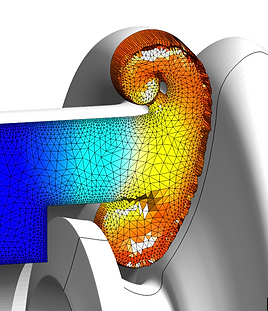